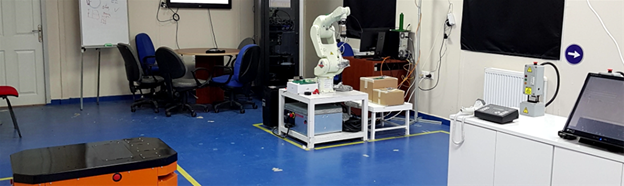
The use of industrial robots in the industry reached to 2.7 million in 2020 according to the world robotics industrial robots report [1]. This number is expected to rise due to fact that robots become indispensable elements of smart production with the fourth industrial revolution. The requirement of a faster and more efficient production process emerges the usage of more robots in factories in various fields such as automotive, electronic, food, etc. Industrial robots are involved in tasks such as assembly, painting, welding, quality control etc. They have showed their success for performing iterative jobs with higher performance. In this new era, moving from automation to autonomy will also bring new opportunities for industrial robots. This new autonomous robots percept the environment, makes a plan and act depending on the perception. This autonomy also brings some barriers for widespread application of these new robotic systems. The robotic systems should be trusted before usage. Therefore, developing new verification & validation methods for the safety and security of new autonomous robots is critical for their wider application in the shopfloor.
Verification and Validation Methods for Robotic Systems
Verification & validation of robotic systems is a challenging problem due to their complex and interactive architectures. Successful operations of robots are not only depending hardware and software components but also their interaction with the environment. Robots are systems that contains both mechanical and electronic hardware components. For the successful interaction with the environment, robots use sensors to perceive their environment and actuators that enable them to make changes in the environment. According to these perceptions, algorithms determine the appropriate action and activate the actuators. All these systems; hardware, software, and interaction with the environment should be considered for Verification & validation. Assuming all hardware units are working as expected, at least V&V process should apply to the software component including the interaction with the environment.
Software Engineering standards known as IEEE-STD-610 defines “Verification” as a test of a system to prove that it meets all its specified requirements at a particular stage of its development. On the other hand, “Validation” is defined as an activity that ensures that an end product stakeholder’s true needs and expectations are met. Verification and validation activities are typically performed at many different stages of development process. Early stage focusses more on verification activities like reviews and testing to check that the system is being developed correctly. During final stage, validation activities are often mandatory to check that the system provides its intended services.
There are many approaches like formal methods, simulation-based testing and user validation in experiments for V&V of robotic systems. Simulation-based testing is commonly used one for robotic systems. But, it insufficient to ensure the correctness. Experiments is most solid way, but it is not possible to cover all situations that may exist in the field. Formal methods that are based on mathematical techniques can greatly aid in developing dependable systems. They can be used across all phases of the system development life cycle including verification and validation [2]. The study [3] and the references therein gives a good coverage of are various studies for application of formal methods to V&V of Robotic Systems. It firstly summarizes the studies from a software engineering point of view. Then, focus on external and internal challenges specifically related to environment interaction and decision respectively. Some of the most common formal verification techniques are model checking [4] and theorem proving [5]. Some common model checking tools used for robotic studies are PRISM, NuSMV and UPPAAL. On robotic side Robot Operating Systems (ROS) [6] is one of the widely used open source tool to integrate the V&V tools. The ROS and UPPAAL is integrated in [7] for V&V of Robotic systems. On the other hand, formal methods may also not be enough due to the uncertain environment and dynamic nature of the system at runtime. Runtime verification (RV) is rather a lightweight formal verification technique that attempts to monitor whether the target system satisfies expected behaviors [8]. The main advantage of RV compared model checking approach is reduction in expanded number of states. A runtime verification framework is also developed for robotic applications on top of the ROS [9]. The study [10] provides a good overview of V&V methods including formal verification, simulation-based testing and experiments considering human-robot interaction problem. Therefore, multiple V&V methods are required to ensure a complete certification process.
References
[1] IFR, 2020, World Robotics Report 2020, web site: https://ifr.org/ifr-press-releases/news/record-2.7-million-robots-work-in-factories-around-the-globe
[2] R. Sinha, S. Patil, L. Gomes, V. Vyatkin, 2019, A Survey of Static Formal Methods for Building Dependable Industrial Automation Systems, IEEE Transactions on Industrial Informatics, Vol.(7) 1, pp. 3772-3783.
[3] R. Wang, Y. Wei, HB Song, Y. Jiang, Y. Guan, XY Song, XJ Li, 2019, Formal Specification and Verification of Autonomous Robotic Systems: A Survey, ACM COMPUTING SURVEYS, Vol.5 2(5), Article:100.
[4] E.M. Clarke, O. Grumberg, and D. A. Peled, 1999, Model Checking. Cambridge, MA, USA: MIT Press.
[5] M. Fitting, 1996, First-Order Logic and Automated Theorem Proving. New York, NY: Springer.
[6] ROS, Robot Operating Systems, Open Source Robotics Foundation (2019) , Available at: http://www.ros.org/ (accessed 22 May 2021)
[7] R. Halder, J. Proenca, N. Macedo, A. Santos, 2017, Formal Verification of ROS-based Robotic Applications using Timed-Automata, Proceedings of 5th IEEE/ACM International FME Workshop on Formal Methods in Software Engineering (FormaliSE), pp.44-50.
[8] C. Hu, W. Dong, Y. Yang, H. Shi and G. Zhou, 2020, Runtime Verification on Hierarchical Properties of ROS-Based Robot Swarms, IEEE Transactions on Reliability, vol. 69(2), pp. 674-689.
[9] J. Huang, C. Erdogan, Y. Zhang, B. M. Moore, Q. Luo, A. Sundaresan, and G. Rosu, 2014, ROSRV: runtime verification for robots. Lecture Notes in Computer Science, Vol. 8734, pp.247–254. Springer.
[10] M. Webster, D. Western, D. Araiza-Illan, C. Dixon, K. Eder, M. Fisher, AG. Pipe, 2020, A corroborative approach to verification and validation of human–robot teams, The International Journal of Robotics Research, Vol. 39(1), pp.73–99.
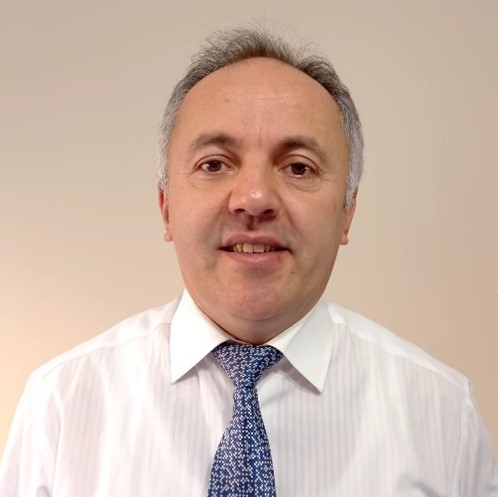
Ahmet Yazıcı, Center for Intelligent Systems Applications Research (CISAR) at ESOGU
Ahmet Yazıcı received the Ph.D. degree from Eskisehir Osmangazi University (ESOGU) in control systems in 2005. He was a member of the OSU-ACT Team in 2007 Darpa Urban Challenge. He is full time professor within the Department of Computer Engineering, ESOGU. He is founder of Intelligent Factory and Robotic Laboratory (2016) and Center for Intelligent Systems Research (CISAR) (2020). He is also currently director of CISAR which has good cooperation with Large Industries, SMEs and Research Institutions for industry-driven projects
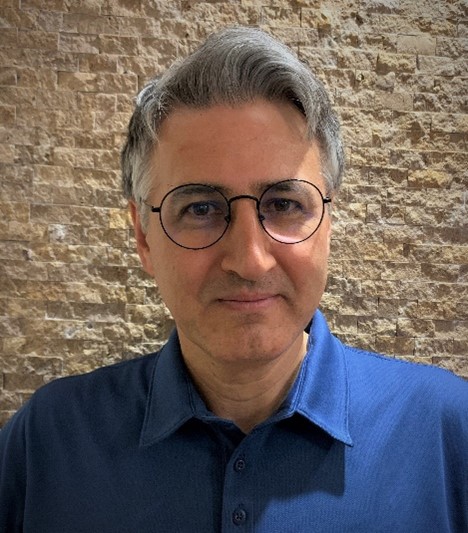
Dr. Metin Özkan, associate professor in the department of computer engineering at Eskisehir Osmangazi University, Eskisehir, Turkey. He received the B.S., M.S., and Ph.D. degrees in the department of Electrical-Electronics Engineering. His interests include mobile and industrial robotics, multi-agent systems, control systems, and industrial automation.
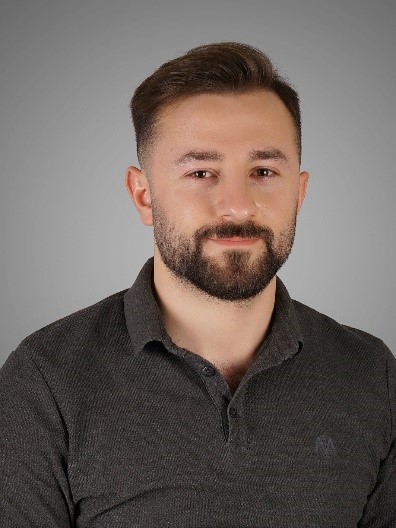
Zekeriyya Demirci, Research Assistant at Eskişehir Osmangazi University (ESOGU).
He received his bachelor’s degree from ESOGU Computer Engineering Department in 2020 and also started his master’s degree education on robotic. Currently, he is working as a research assistant at ESOGU and has an interest such kind of fields like machine learning and data science. In addition, he is contributing to VALU3S in the research and development of verification and validation methods and tools. His research on this project focusses specifically on the safety of industrial robots.